Our Services
Repair ● Maintenance ● Calibration ● Training ● Educational Programs
Efficient and effective in managing your repair process
Traditional industrial assembly tool repair has always been reactive. Rhino Tool House is focused on Revolutionizing Your Process, by focusing on proactive preventative maintenance, calibrations, and repairs.
Rhino Tool House has the people and processes in place to be your complete industrial solutions provider which is how we can we provide expert repairs, maintenance, and calibration services for virtually any industrial tool on the market, regardless of the brand or the type of tool. And that includes product you bought from us and product you purchased elsewhere.
All of our repair centers, strategically located across the US, are ISO/IEC 17025:2017 accredited. In fact, because of our rigid quality systems and procedures that ensure quality and repeatability, we received zero Non-Conformance Reports (NCRs) in our latest ISO audit. Rhino Tool House can build a strong and lasting partnership with you and your team to give you service support that out-performs virtually every other service option in the country.
Remember, too, when it’s not convenient or practical to send out your tools, we can come to you to perform on-site calibration. You can even have a permanent technician stationed right at your facility, just as we’ve done with several manufacturers across the U.S.
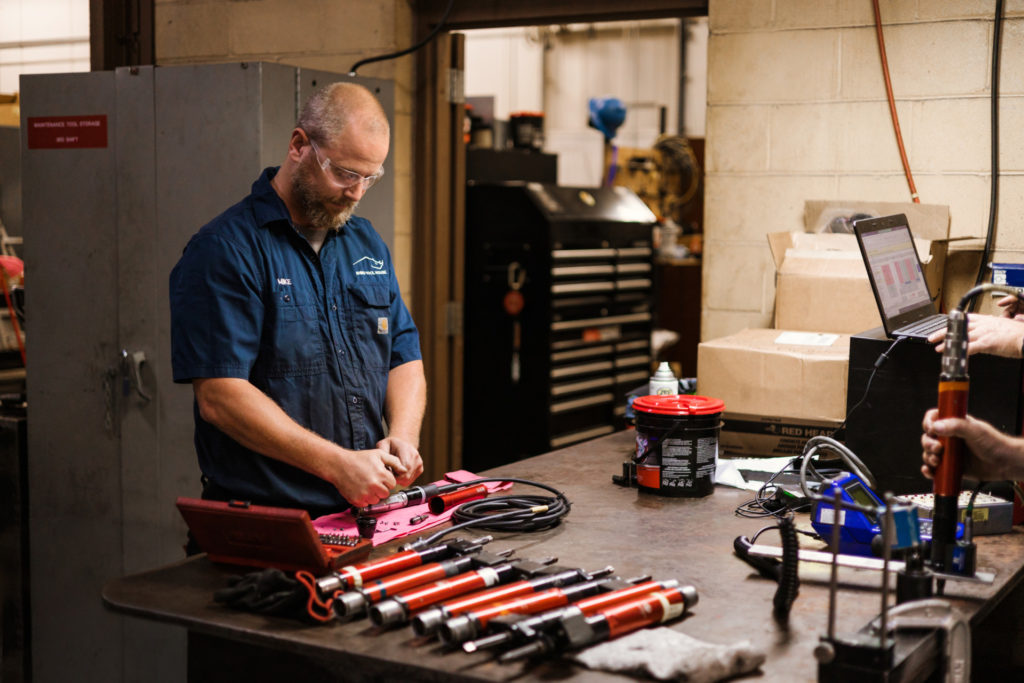
Tool repair and maintenance
With three repair centers across the country, we are strategically located to provide professional and efficient tool repairs. We service every major brand, every major tool type. Rhino Tool House can build a strong and lasting partnership with you and your team to give you consistently efficient and effective repair process management.
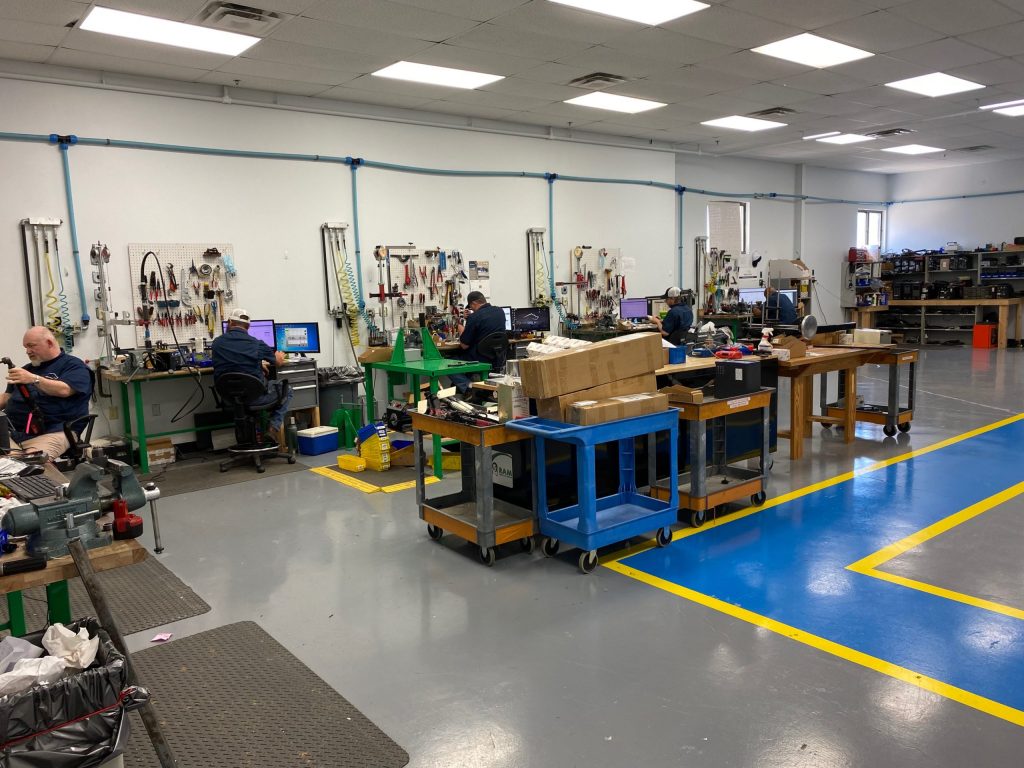
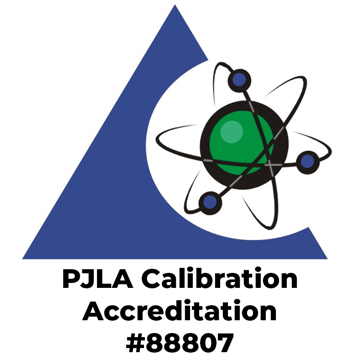
Calibration
With ISO/IEC 17025:2017 accreditation standards, you’re assured your tools are technically sound and able to perform to specifications accurately and proficiently.
On-site services
When it’s not convenient or practical to send out your tools to a remote location, we come to you. We can even station a technician right at your facility to help keep you up and running, 24/7. Our ISO/IEC 17025:2017 accreditation carries over to your facility. Minimize travel and down time by having a Rhino Tool House technician come to you. We can perform the work during scheduled downtime, non-peak shift hours, or customize a plan to meet your plant specific schedule!
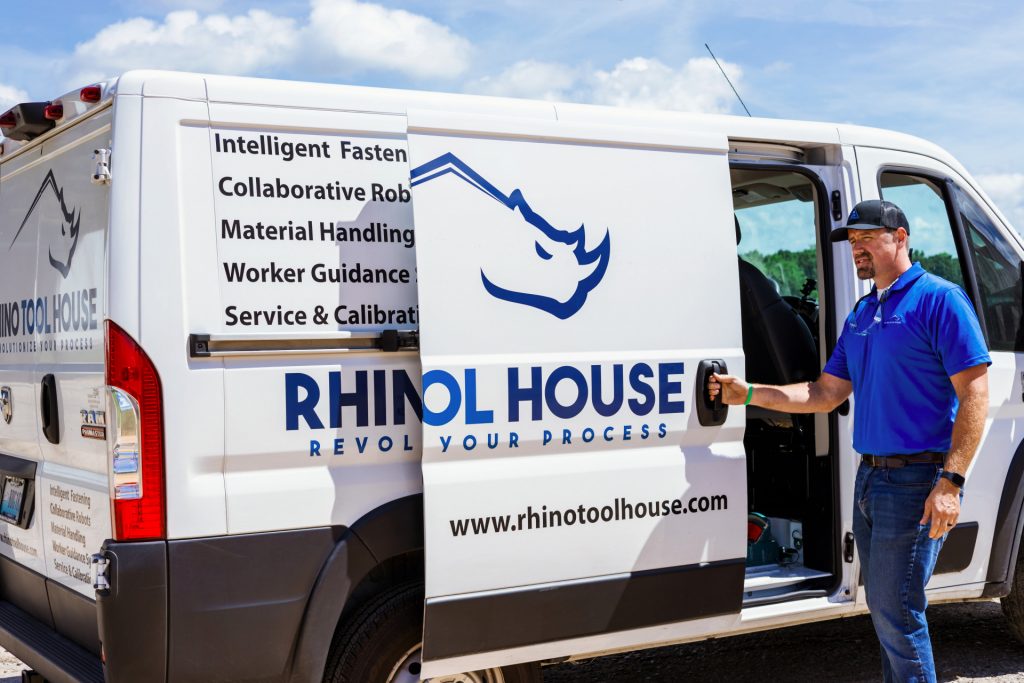
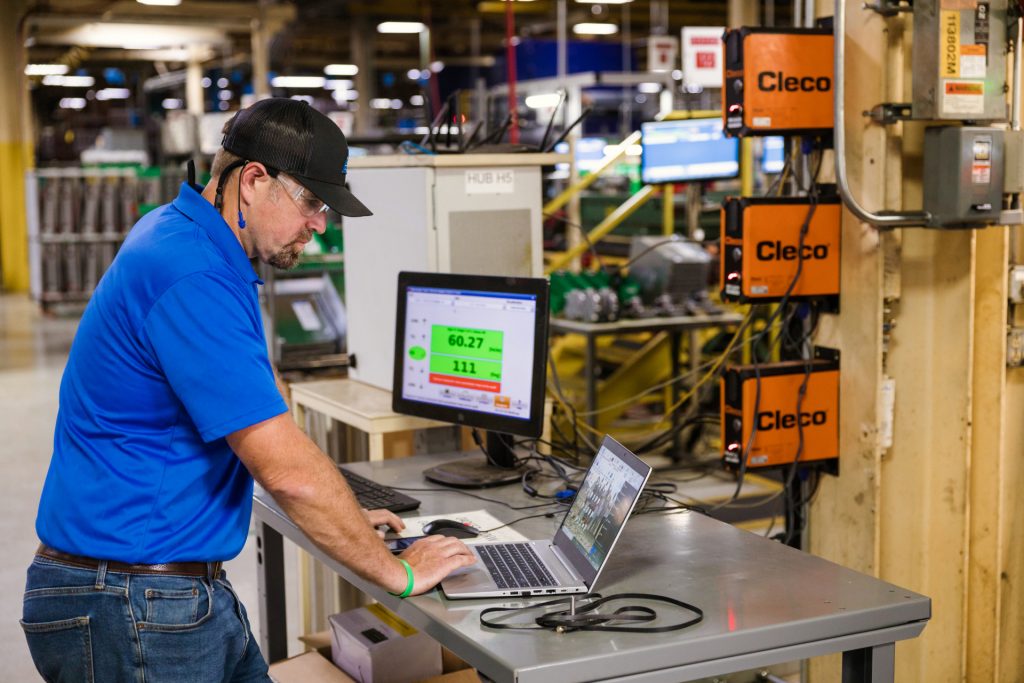
RepairTracker247
Because our goal is to help you revolutionize your process in every way possible, we can also help you establish a customized, in-house tool-management program to track and manage your tool repairs. REPAIRTRACKER247 is a web-based, plant-wide snapshot of your repairs that helps you initiate, manage, and track your repairs from beginning to end. It saves time, saves unnecessary costs, and helps make sure you stay up and running for as long as possible.
Training and education programs
- Fastening Technology
- Industry 4.0
- Augmented Reality
- Error-Proofing
- Collaborative Robots
- Ergonomics
- Wearables
- Hardware
- Software
- Service & Repair
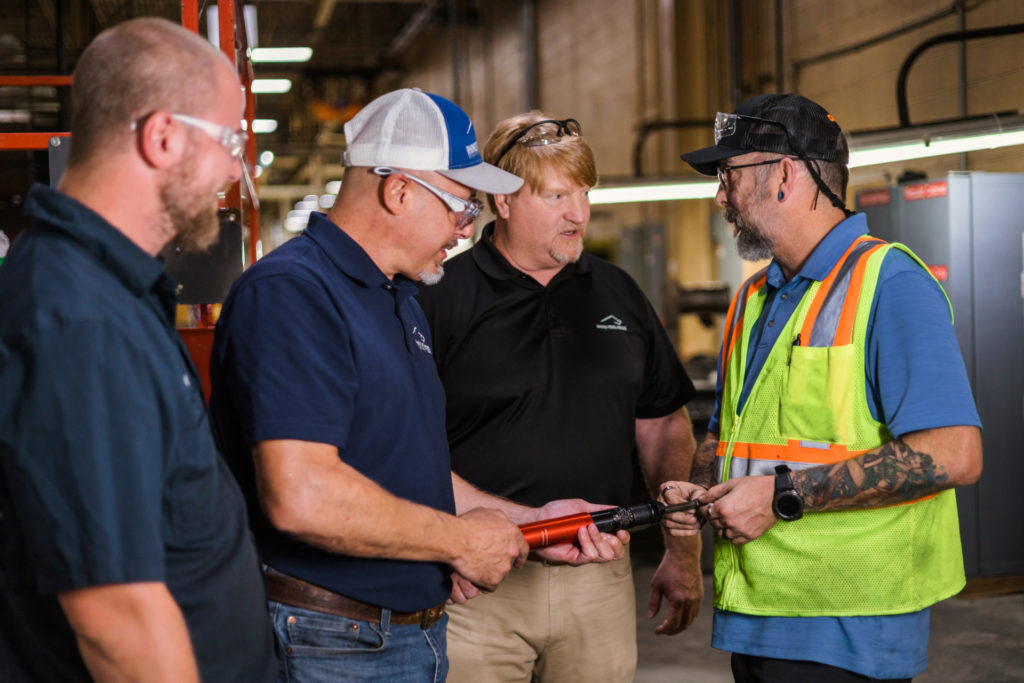